How Often Should Test and Tag Be Done in Queensland?
What Does Test & Tag Refer To?
Test and tag is an essential practice for maintaining electrical safety in various environments, ensuring that equipment is safe to use and reducing the risk of electrical accidents. The process involves thorough inspection and testing of electrical equipment to ascertain its safety and adherence to current electrical safety standards and regulations. Regular test and tag guarantees the safety of electrical appliances and upholds continuous safety standards.
Test and Tag Purpose and Benefits
- Safety: The primary goal is to ensure the safety of users by identifying and rectifying any potential electrical hazards.
- Compliance: In many workplaces, regular testing and tagging are required to comply with occupational health and safety regulations.
- Maintenance: It helps in the proactive maintenance of equipment, potentially extending its lifespan by identifying issues before they lead to equipment failure.
Two Step Process for Testing
Step One - is a visual inspection of the equipment for any faults. Checking will include
- Missing insulation
- Signs of overheating or burning
- Damaged cords and plugs
- Visible damage or wear
Step Two - is electrical testing, if the visual inspection is satisfactory the equipment will undergo electrical testing using specialised equipment. The tests include
- Polarity Test - confirms the wiring of the plug and appliance is correct
- Earth Continuity Test - Ensures the earth wire in the device is properly connected and can carry fault current safely.
- Leakage Current Test - Checks for any unintended current flow from live parts to the earth or any exposed conductive parts.
- Insulation Resistance Test - Measures the resistance of the insulation to ensure it is not damaged and is providing adequate protection.
Two Step Process for Tagging
Step One - Once the equipment passes the tests, it is tagged with a durable colour label. Each label and colour indicates the month the equipment was tested and adheres to the Australian Standards used for testing and tagging in Qld AS/NZS 3760:2022. Tag information includes
- The date of testing will be identified with a specific colour tag.
- The next test due date
- The name of the person who performed the test
- A unique identifier for the equipment
- The status of the equipment (e.g., "Passed" or "Failed")
Step Two - Detailed records of the tests and results are documented and maintained. This helps in tracking the equipment's safety status and scheduling future tests.
Who Can Conduct Test and Tag?
In Queensland, test and tag procedures are regulated by WorkSafe Qld. Only individuals designated by their employer as competent are permitted to conduct tests and tag on electrical equipment. Competence is determined by the individual's knowledge, skills, training, experience, or qualifications. You may think that all electricians are automatically qualified to conduct test and tag, however this in not the case. Even though they have a broad understanding of electrical systems, specific training and certification are often required to legally and competently perform test and tag procedures. Let's examine the two scenarios for test and tag and the specific requirements for each.
Testing and Tagging Your Own Equipment
- Complete a Nationally Recognised Test and Tag Course
- Work with AS/NZS 3760 or 3012 Standards
- Maintain competency and adhere to all Queensland state regulation and guidelines
Providing Test and Tagging Services for Others
- Complete a Nationally Recognised Test and Tag Course and/or Test and Tag Business Course if required
- Apply to the Queensland Electrical Safety Office for a Restricted Electrical Contractors Licence
- Work with AS/NZS 3760 or 3012 Standards
- Maintain competency and adhere to all Queensland state regulation and guidelines
Frequency of Test and Tag
How often you have test & tagging done varies on the type of equipment and the environment in which it is used. Examples are:
- High-risk environments -such as construction, building and demolition sites may require more frequent testing. The recommended time frame is every 3 months to 12 months. Factories, warehouses and production recommended 6 monthly
- Low-risk environments - include offices that generally have longer intervals between tests with recommendations of every 1 to 5 years . An environment where the equipment / supply cord is proneto flexing or open to damage recommended 12 months. If the equipment / supply cords are not prone to flexing or open to abuse recommended 5 years
Cost of Test and Tag
The cost of test and tag in Queensland varies and typically depends on the location of where the test and tag will be conducted, the number of items to be tested and the provider. A rough price guide would be between $3 to $10 per item. However, the cost should be discussed with the provider who may offer discounts for ongoing contracts or based on the volume of items.
If you need more information on Test and Tag or require the services of a qualified test and tag electrician please contact the team at Urban Energy on 0485 814 490. Alternately you can complete our online enquiry form.
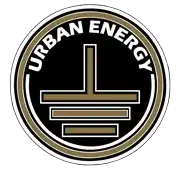
Source:
Testing and tagging of electrical equipment | WorkSafe.qld.gov.au
Test and Tag Regulation in QLD: Complete Guide (testandtagtraining.com.au)